Importance of Proper Inlet Location on a Screw Conveyor
Question
I am assembling my screw conveyor in the field and am in the process of installing the inlet. Are there any restrictions as to where I put the inlet, or can it be installed anywhere?
Answer
It may seem as though an inlet may be installed at any location along the screw conveyor but there are some key details to consider. Inlet location is important for a proper functioning screw conveyor. Installing the inlet too close to the end of the trough can cause material to compact and stagnate in the area between the trough end and screw flights and not get conveyed downstream. CEMA standard clearance between the end of the flights and the trough end range from 3/4 to 2-1/2 inches. Because of this clearance, there is a dead area at the end of the conveyor where the flight does not convey material. Most screw conveyors are designed to CEMA standards for both inlet and discharge location. For example, a 12-inch screw conveyor has a minimum distance between the end of trough and the center of inlet of 10-1/2 inches. Please refer to the KWS Engineering Guide on our website.
Often times, inlets get installed at the very end of the trough causing problems with bulk material conveying. KWS recently solved two problems in the field from other manufacturers because of improper inlet location. After KWS recommended that the inlet be moved to the CEMA minimum distance, conveyor efficiency improved, and downtime was eliminated. You can rely on the technical expertise of KWS to solve any bulk material handling problem.
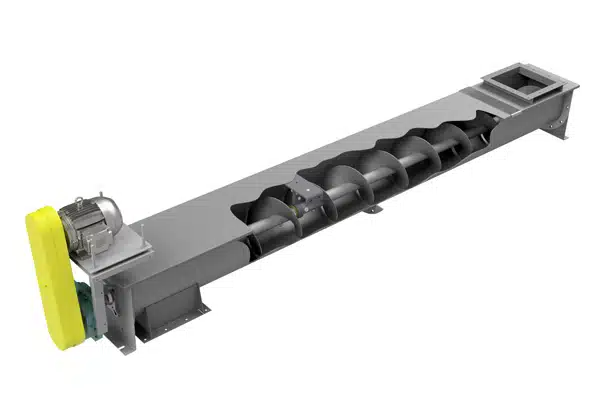
Inlet is Located in Proper Location in Accordance with CEMA Standards