Shear Pin Sprockets for Screw Conveyors
Question
I have a screw conveyor in my plant that gets overloaded on occasion and causes a screw failure. Is there a shear pin mechanism to avoid damage to the screw during an overload condition?
Answer
All KWS screw conveyors and components are engineered to withstand more than the full motor torque of the system. The KWS design method eliminates the need for a shear pin mechanism, which is typically used to prevent damage under excessive load. By incorporating a 5-to-1 safety factor in the design of all screw conveyor components, KWS ensures that your screw conveyor will handle significantly more than full motor torque. This safety margin is crucial for maintaining the integrity and reliability of the equipment under various operating conditions. If a screw conveyor becomes overloaded, the motor will experience an increase in amperage draw until the motor overloads and “amps out.” No mechanical failures occur. The drive arrangement is typically directly coupled to the screw conveyor input shaft using a screw conveyor drive or helical bevel gearmotor.
If you absolutely must have a shear pin arrangement for your screw conveyor, there are several design considerations. First, you must have an inline gear reducer with a chain-and-sprocket secondary drive. The drive unit is offset to the screw conveyor on a separate drive base and a chain guard is required for safety purposes. The shear pin is located in the larger diameter sprocket or driven sprocket. The shear strength of the shear pin will have to be determined based on full motor torque and loading conditions.
The costs of using a shear pin drive arrangement are much greater than a direct drive arrangement. Our goal is to provide equipment that exceeds your operating specifications and reduces maintenance and downtime. KWS’ comprehensive approach to design and safety underscores our commitment to producing high-quality, reliable equipment.
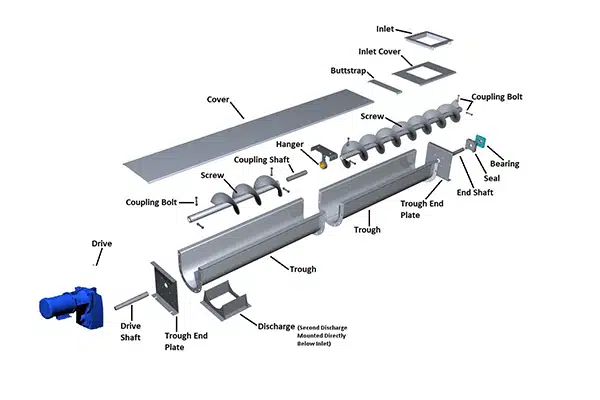
Every KWS Screw Component is Designed to Withstand More Than Full-Motor Torque with an Additional Safety Factor of 5-to-1
KWS Recommends Use of Direct Drive Reducers for Most Applications
Inline Gear Reducer is Required for Use with Chain-and-Sprocket Secondary Drive
Shear Pin is Located in Larger Diameter or Driven Sprocket
Shear Strength of Shear Pin is Based on Full Motor Torque and Loading Conditions