Direct-Shaft Mount Drive Design
The KWS direct-drive shaft mount design offers a compact and cost effective alternative when compared to traditional belt-driven screw conveyor drives. Parallel helical or helical-bevel gear reducers with C-face adapters or gear motors are available. The gear reducer utilizes a hollow bore to accept a drive shaft manufactured by KWS or the drive manufacturer. The drive shaft couples directly to the screw.
The KWS direct-drive shaft mount design can be mounted directly to a standard CEMA trough end or a bulkhead trough end, depending upon the application.
Features
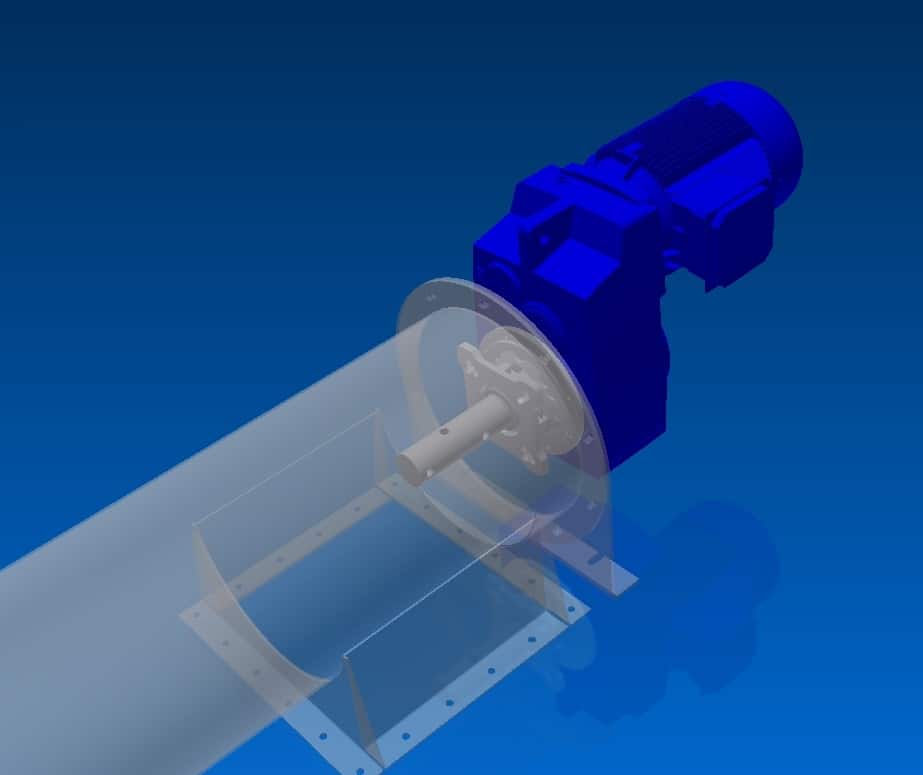
Variety of Shaft Materials – Drive shafts are available in C1045 or C4140 carbon steel for industrial applications and 304 or 316 stainless steel for corrosive or food-grade applications.
Variety of Gear Reducer Arrangements – Parallel shaft and helical-bevel right angle gear reducers are available to meet the space constraints of any application.
Variety of Shaft Seal Options – Flanged gland seals with multiple rings of packing, air or nitrogen purged seals, food grade seals or even mechanical seals can be used with the bulkhead trough end option.
Benefits
Simpler Drive Package – The KWS direct-drive shaft mount design provides fewer components and reduces the footprint when compared to other drive arrangements. There are no belts to frequently replace or noisy chains to maintain and lubricate. Rotational speeds can be fine-tuned by using a variable frequency drive (VFD). VFDs provide infinite speed adjustment and are more flexible than the traditional method of changing sheaves or sprocket sizes to change conveyor speeds.
Ease of Maintenance – The KWS direct-drive shaft mount design can be easily accessed for maintenance and replacement. Fewer drive components require less maintenance and fewer items to keep on the shelf. The reduction in cost for spare parts and maintenance downtime results in significant cost savings over the life of the drive.
Better Performance – The KWS direct-drive shaft mount design is more efficient due to the direct coupled design. Drive efficiency can be further increased by using energy efficient motors. Belt or chain drives have lower total drive performance and efficiency.