Improved Screw Design for Rail Car Unloading at Nestle Purina
Pet food is made from a mixture of many ingredients such as barley, soybean meal, wheat, and minerals. These ingredients are transported in rail cars to pet food processing plants and unloaded using screw conveyors. The ingredients are then transferred into the plant for further processing. Nestle Purina needed a solution for their railcar unloading screw conveyor, which was failing periodically. A solution was critical because all ingredients start in the unloading process. A failure could be very costly and affect all processes downstream.
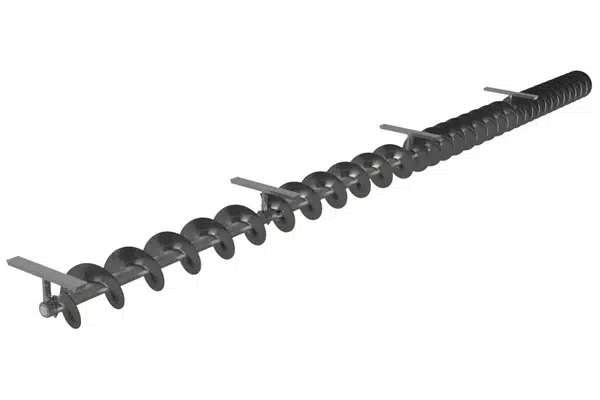
New KWS Design Eliminates Down Time
Challenge
Nestle Purina’s existing unloading screws were breaking at the pipe and shafts. Ingredients would bridge and the screw would fail at the drive end. Nestle Purina contacted KWS because they were happy with the quality and service provided at another Nestle Purina location. KWS engineers visited the site to analyze the existing unloading conveyor and provided a solution.
KWS Advantage
KWS improved the screw design with larger diameter pipe with heavier wall thickness, larger shaft size, and variable pitch flights. Larger diameter pipe and shaft greatly increase torque rating and resistance to the weight of the flood feeding material. Variable pitch screws promote mass flow metering. KWS created engineered drawings and documented every detail showing the improvements. KWS provided the complete design and equipment within 4 weeks of the site visit. The innovative design eliminates downtime and increases the life of screws with an annual cost savings of over $100,000.00 per year.
Testimonial
"The new and improved KWS Unloading System has been working out great! Thanks for the excellent work!"
Rick Bushman, Maintenance Supervisor – Nestle Purina PetCare Company
Variable Pitch Screws Promote Mass Flow
Cost Savings of Over $100,000.00 per Year with New KWS Design