Complete Storage and Conveying System for Spent Catalyst
Alpha Omega Recycling, Inc.
Longview, TX
General Description
Alpha Omega Recycling provides processing services for waste materials that contain metal byproducts. In partnership with Amlon Resource Group, Alpha Omega manages and recycles spent catalysts and other metal-bearing wastes. Catalysts are used in refining petroleum to increase the speed of chemical reactions. Catalysts often contain metals, metal oxides, or sulfides. When catalyst is no longer usable it is known as spent catalyst. It can then be sent to Alpha Omega for processing to recover leftover metals. The metals can be recycled or are disposed of in an environmentally friendly way.
Amlon Resource Group has a new proprietary technique for processing spent catalysts and contacted KWS for the design and supply of the material handling and storage system. KWS provided a complete material handling system that interfaced with bulk container unloading equipment, screeners, thermal processors and bulk bag loading equipment.
Design Parameters
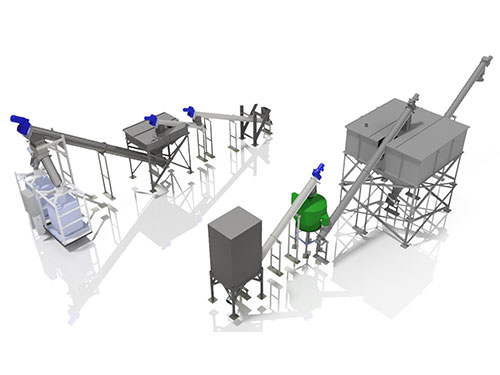
KWS Provided a Complete Conveying System for Catalyst
- Product Type: Spent Catalyst
- Material Density 45 to 90 Lbs. per Cubic Foot
- Conveyor System Capacity: 90 Cubic feet per hour
- Duty: Intermittent
KWS Advantages
A team of engineers from KWS traveled to Alpha Omega and gathered critical information about the new process and to determine the layout of the new conveying system. The equipment supplied by KWS had to integrate with other process equipment. KWS provided engineering services including complete system design. KWS is unique in the market and can provide engineering services as well as equipment supply. KWS engineers visited Alpha Omega again during the approval drawing process to assist Alpha Omega and to confirm all dimensional information for proper installation.
Special Features
KWS designed and provided a very rugged system to handle the challenges of the application. Abrasion resistant AR400 material was chosen for the flights and trough liners in the new screw conveyors and feeders due to the highly abrasive nature of the catalyst. Trough liners also reduce the clearance between the screw and trough, improving efficiency while conveying up steep incline angles.
The screw feeders and conveyors were designed to meter and convey a wide variety of bulk materials of varying densities and flow rates. Drive units were designed to generate maximum torque for handling any type of upset condition.
KWS designed and manufactured all hoppers, supports and chutes for the system. Hoppers were designed for maximum volume and mass flow. The system bolted together with no field modifications. Adjustable structural supports allowed for versatility to achieve final fit-up in the field. KWS also provided structural supports for the vibratory screener and thermal processor. KWS purchased a two-way diverter from Vortex Valves for the bagging process.
Testimonial
"The new system is performing great. We will use KWS for our future expansion."
Jack Blonquist, Director Thermal Operations, Amlon Resource Group (2019)
Spent Catalyst is Delivered in Rigid Bulk Containers
Spent Catalyst is Metered into Process with a KWS Inclined Screw Feeder
KWS Inclined Screw Feeder Meters Spent Catalyst to Further Processing
KWS Inclined Screw Conveyor Conveys Processed Catalyst to Surge Hopper
Surge Hopper Provides Extra Capacity for Continuous Process
Two Bulk Bags are Filled Through Diverter Gate and Chutes