Conveying Grape Waste at Winery in Salt Lake City, Utah
General Description
The wine industry is a multi-billion-dollar industry that is prevalent in the western part of the United States. There are currently over 11,000 wineries in the United States, and the industry expects an annual growth rate of over 5-percent per year for the next seven years.
Depending on the type of wine being produced, grapes are pressed at various times in the wine making process to separate juice from pomace. Grape pomace consists of grape skins, stems, and seeds. Marquise OSI Winery was building a new facility outside of Salt Lake City, UT and required a custom screw conveyor system to install underneath their grape presses and transport grape pomace to a bin for use as an ingredient in animal feed. KWS designed and engineered a long-lasting custom conveying solution to meet all of Marquise OSI Winery’s requirements.
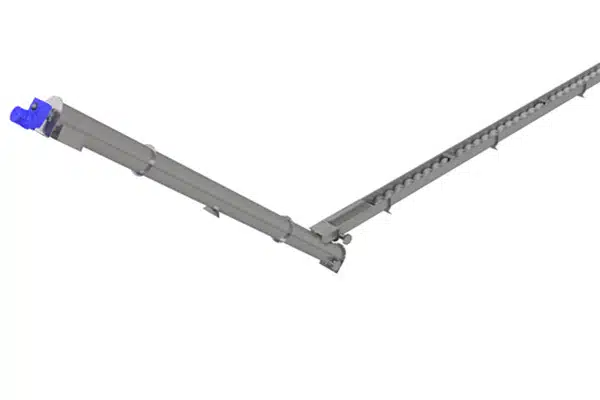
KWS Screw Conveyors Transport Grape Pomace from Presses to Containers
Design Parameters
- Product Type: Grape Pomace
- Material Density: 30 to 45 Lbs. per Cubic Foot
- Capacity: 20,000 Lbs. per Hour
- Duty: 24 Hours per Day, 7 Days per Week
KWS Advantages
With extensive technical and application experience, KWS provided a custom solution for a unique application on an expedited timeline. KWS provided 3D CAD models of the entire system during the design approval process which included the wine presses to ensure proper alignment, placement of the screws, and understanding project requirements. The building and the pit beneath the presses were also modeled to confirm that the design would fit within the required space constraints. KWS ensured that the equipment could be installed without unexpected field modifications to the equipment, building, or support structures.
Screw Conveyor is Located in Pit and Receives Grape Pomace from Presses
KWS Special Features
Stainless steel construction was used to prevent corrosion, and continuous welds were provided to prevent debris from building up between the pipe and flight connection. Flush out ports were added to the side of the troughs to allow residual grape juice and cleaning fluids to drain freely. Hip roof covers were used on the conveyor section located outside the building to prevent rain from collecting on the housing. To work within the required space constraints, a shafted horizontal conveyor was custom designed to feed directly into an inclined shaftless conveyor in place of using a CEMA standard inlet and discharge connection. The shaftless conveyor utilized a dual spiral shaftless screw to ensure that the grape pomace conveyed easily up the incline.
Testimonial
"KWS provided a great solution that is working well. We are extremely happy with the turnout."
Rick Neria – Material Handling Consultant
Horizontal Pit Conveyor Feeds Directly into Inclined Conveyor
Shaftless Conveyor Efficiently Conveys Grape Pomace on Incline