Inclined Screw Feeder for Metering Food Powders SensoryEffects in Defiance, OH
SensoryEffects Powder Systems
Defiance, OH
General Description
SensoryEffects is a leading supplier of foods and food ingredients. Many of the products produced by SensoryEffects are used for making baked goods, beverages, cereals and snacks. Powdered dairy creamers, solid and liquid flavorings, emulsified powders and baby formulas are just a few of the many products produced. SensoryEffects needed a solution for metering a food powder into a blending process. Screw feeders were the perfect solution to accurately meter the powder from a storage hopper and discharge into blenders. The powders are sold to food and beverage manufacturers and distributors across the United States. KWS provided a cost effective, long term solution for the application.
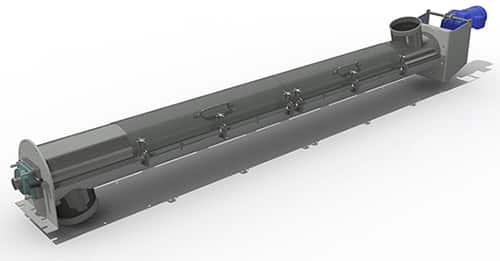
ISO View of Inclined Screw Feeder
Design Parameters
- Product Type: Cocoa Powder and Coffee
- Material Density: 15 to 30 Lbs. per Cubic Foot
- Capacity: 400 Cubic Feet per Hour
- Duty: 24 Hours per Day, 7 Days per Week
KWS Advantages
Engineers from KWS worked together with the SensoryEffects corporate project engineer and plant manager to create the ideal solution for their plant in Defiance, OH. The collaboration produced a system that was perfectly designed, manufactured and delivered before the expected date. KWS provided knowledge, workmanship and solutions to the project.
Hinged Covers Allow for Cleaning After All
Power is Shut Off and Locked Out/Tagged Out
Special Features
As this is a food grade application, the new KWS screw feeder was manufactured using 304 stainless steel with all internal welds polished to a smooth 150-grit surface finish free of pits, crack, and crevices. The KWS screw design utilized stepped pitch fighting in the inlet section to promote a controlled, metered feed of the cocoa powder and coffee. KWS provided a special tubular housing for maximum conveying efficiency on a steep incline with hinged covers for easy maintenance of the screw for frequent cleanout. SensoryEffects provided interlocking safety switches on the covers after the unit was installed for operator safety.
Special air-purged shaft seals were used to contain the food product within the screw feeder. A KWS torque arm trough end with floating drive unit was utilized to accept any run out of the screw and avoid any binding caused by the rigid shrink fit and seal welded drive shaft when mounted to the shaft mounted reducer.
Tail End of Screw Feeder with Air-Purged Shaft Seal
Drive End of Screw Feeder with KWS Torque Arm Trough End with Floating Shaft Mount Drive