KWS Redesigns Bucket Elevator to Double Capacity at CertainTeed in Portland, OR
General Description
CertainTeed Corporation, a subsidiary of Saint-Gobain, is one of the largest manufacturers of roofing shingle products in North America. Demand for CertainTeed products has continued to grow, and the roofing shingle manufacturing plant in Portland, OR needed to increase capacity to meet the market’s needs. During the shingle making process, bucket elevators are used to lift bulk materials such as sand, silica, and roofing granules vertically from feeders to silos where they are stored before entering the production process.
CertainTeed had been utilizing an undersized bucket elevator for the current demand causing product to fall out of the buckets and fill the bottom of the elevator with material. This issue required operators to spend countless labor hours opening the bottom of the elevator and cleaning out the unused product. CertainTeed looked to KWS to design and manufacture a bucket elevator for their increased capacity and reduce loss of product. Due to lack of space, the new bucket elevator had to be custom designed to fit in the existing area while increasing capacity. KWS provided a solution that met and exceeded CertainTeed’s requirements.
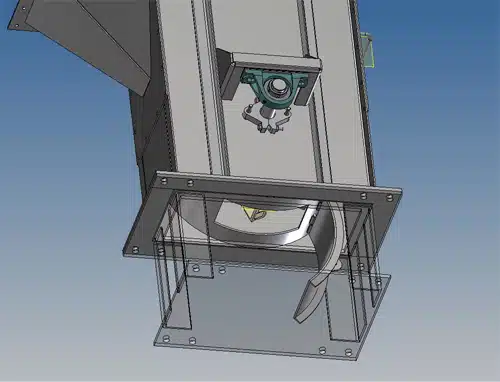
Curved Bottom Plate Creates Close Clearance in Boot Section
Design Parameters
- Product Type: Roofing Granules
- Material Density: Grit 85 to 95 Pounds per Square Foot
- Capacity: 680 Cubic Feet per Hour
- Duty: 24 Hours per Day, 7 Days per Week
KWS Advantages
KWS has had many successful projects at CertainTeed plants across North America. The engineers at CertainTeed worked with the engineering team at KWS to find a solution that met the increased capacity requirements while using less space than a standard bucket elevator would typically allow. Several site visits were made to survey the application and take exact measurements. 3D models of the area were created to make sure the new equipment would fit into the existing space.
KWS Special Features
KWS designed and manufactured a unique bucket elevator for this project. The bucket elevator was designed to deliver twice the capacity in the same casing size as the existing elevator. The new KWS bucket elevator was installed quickly with a few minor modifications to existing structure. KWS and CertainTeed designed a unique pneumatically controlled clean-out door for ease of access for routine maintenance. Since grit is extremely abrasive, abrasion resistant plate was installed on the inside of the head and boot sections to prevent wear and increase the life of the equipment.
KWS located the belt adjustment take-up in the head section, creating close clearance between the buckets and curved bottom plate of the boot section. Close clearance eliminates material buildup in the boot section and greatly reduces maintenance time.
Testimonial
"KWS worked through some difficult issues with limited space while increasing capacity. It took a few modifications, but the new bucket elevator is exceeding capacity and is very ruggedly built. We will be replacing another bucket elevator soon and KWS is our Go-To company."
Mark Delay, Account Manager – MiMotion
Material Fell Out of Buckets and Filled Boot Section
Existing Bucket Elevator was Worn Out and Could Not Meet Capacity
Redesigned KWS Bucket Elevator Doubled Capacity in Same Footprint
Head Section Take Up Allows Close Clearance Clean Out in Boot Section
CertainTeed Added a Clean-Out Door to Existing Bucket Elevator to Clean Out Boot Section