Screw Feeder for Metering Wood Chips into Furnace to Produce Activated Carbon
National Carbon Technologies
Gwinn, MI
General Description
National Carbon Technologies, a leader in carbon products produced from renewable biomass, operates the largest advanced biocarbon production facility in North America. With capacity to convert hundreds of thousands of tons of biomass into patented carbon products, one of National Carbon Technologies’ flagship products is activated carbon. Activated carbon is used for air and water purification, wastewater treatment and many other industrial applications.
Waste wood chips and saw dust are used to produce activated carbon at the Gwinn, MI facility. An existing screw feeder was a constant maintenance issue and caused unexpected down time. The high heat from the furnace was warping the screw feeder causing failures and frequent maintenance was required to keep operating. KWS provided a new, high-temperature screw feeder to meter wood chips and saw dust from a hopper into a furnace.
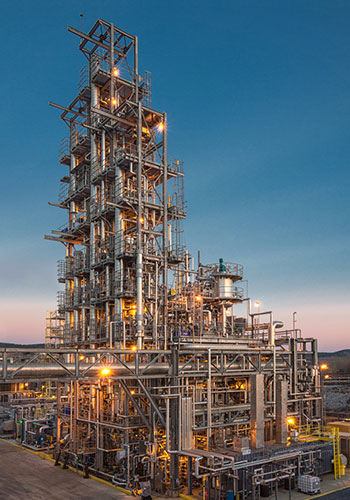
National Carbon Technologies Plant in Gwinn, MI
Design Parameters
- Product Type: Wood Chips and Saw Dust
- Material Density: 10 to 15 Lbs. per Cubic Foot
- Design Temperature: : 1,400-Degrees F
- Conveyor System Capacity: 2,700 Cubic Feet per Hour
- Duty: 24 hours per Day, 7 Days per Week
KWS Advantages
KWS has extensive experience with screw feeder design for metering wood chips at high temperature. By analyzing the existing equipment, KWS engineers determined the root causes of the failures and provided long-term solutions to eliminate any future problems. Based on operating temperatures of 1,400-degrees F, KWS used 3D modeling to ensure the new screw feeder would compensate for thermal expansion and install in place without National Carbon Technologies needing to do any in-house modifications to their other equipment.
Special Features
The new KWS screw feeder was made of 316 stainless steel to withstand the high heat coming from the furnace. The screw feeder housing was made from 20-inch schedule 40 pipe to provide a rigid housing for the screw. Screw diameter was selected to account for thermal expansion and avoid interference between the screw and housing. KWS provided a double bearing arrangement on the drive end to support the screw and allow thermal expansion into the furnace. A shaft-mounted reducer with torque arm bracket eliminated any potential alignment issues. The tail end of the screw was located inside the furnace and subjected to 1,400-degrees F. KWS designed and manufactured a special tail end bearing made from Hastelloy to handle the high temperature. Ceramic flange gaskets and seal rope packing kept the screw feeder airtight. Shaft guards on the drive end were supplied to protect operators.
Testimonial
"The new KWS screw feeder is working extremely well and we’ll definitely buy from KWS again."
Don McFadden, Maintenance Planner / Coordinator – National Carbon Technologies
316 Stainless Steel Withstands 1,400-Degrees F Temperature
Double Bearing Arrangement Provides Rigidity and Allows for Thermal Expansion
Special Tail End Hastelloy Bearing Handles High Temperatures